Index
Figure 1 shows the typical case where the break facets are equally-spaced around the circle (360°/16 = 22.5° apart). Their slopes are shown for the main slopes and proportions cited. They are 0.86% and 0.83% deep, respectively, for the pavilion and crown = total of 1.69%.
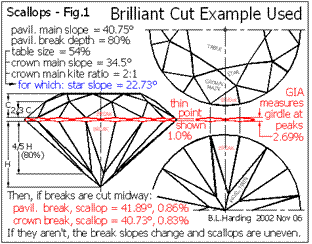
With a girdle thickness of 1.0% at the thinnest points (midpoints) this gives a thickness of 2.7% at the thickest points (endpoints). Some gemologists report one, some report the other; if they report the thinner one you must add 1.7% to the depth of the pavilion, crown, and girdle to get the correct total depth of the stone.
Index
To cut the facets at accurately-spaced angles around the stone (azimuths), most faceting machines use an ‘index wheel’ (called a ‘click wheel’ by most diamond cutters). This is a notched wheel, like a gear, into which a ‘latch’ falls to lock the rotary position of each facet.
Many colored-stone cutters use a variety of index wheels with different numbers of equally-spaced notches. Figure 2 shows the spacings of common wheels = 32, 48, 64, 72, 80, 96, or 120 notches. With a 32-tooth wheel the mains are cut at 4,8,12,16,20,24,28,32 and the stars at 2,6,10,14,18,22,26,30. Usually the break facets are cut halfway between the mains and stars – at 1,3,5,7,9,11,13,15,17,19,21,23,25,27,29,31.
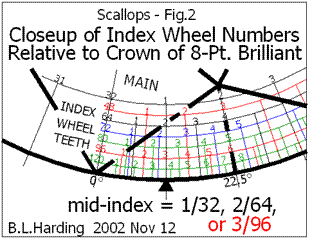
This photo shows an 80-notch index wheel on a Raytech-Shaw faceting machine. This number is used for special cuts
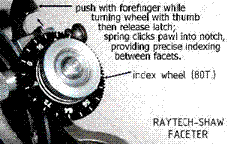
This photo shows a click wheel from a diamond-cutting rig. It has only those notches needed by the brillianteerer for break and star facets.

Photo courtesy of Garry Holloway, 2005 May
Offset Scallops
Figure 3 shows what happens if the scallops are cut at various indexes shown in Fig.2, keeping the same minimum thickness of 1.0% between the pavilion and crown scallops. Note the original example of 0.86% and 0.83%, with equal thickness at both ends, shown in black, when the indexes are equally-spaced and halfway between the mains and stars.
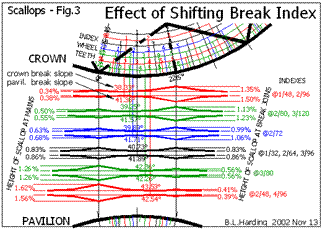
Some cutters do this twisting of break facets intentionally for reasons they deem important. More recently, GIA and AGS have written on this subject as to how it affects the appearance and weight of a diamond.
If the index is closer to the main than to the star index, as shown above the black example, the thickness decreases at the tips of the mains and increases at the join of the break facets.
If it is closer to the star index (at the join of the breaks) than to the main index, as shown below the black example, the reverse is true.
This discussion has been limited to index wheels with a full set of evenly-spaced notches, which is typical of general-purpose faceting machines. It was intended to show that the intentional twisting seen in some diamonds is less than can be provided by such wheels.
For diamond-cutting, click wheels are made with only those teeth necessary and can be made with any spacing the cutter requests from a click-wheel manufacturer.
Figure 4 is of special interest to reduce depth of scallops. On an 8-pointed round brilliant cut with Tolkowsky’s main slopes and standard indexes, as in Fig.1, the combined depth of pavilion and crown scallops is 1.69%. By adding another set of break facets between these, the combined depth of pavilion and crown scallops is reduced to 0.75%. The slopes of the girdle facets are different from Fig.1.
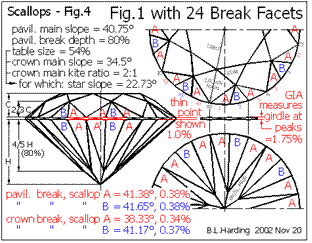
Figure 4b shows an interesting variation; the pavilion and crown are rotated so that the middle break facet of one aligns with the main facet of the other. In this way the thickness variation of the girdle is almost eliminated.
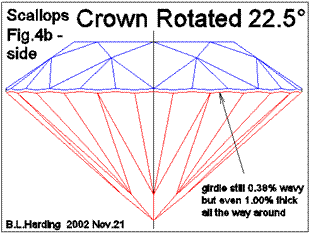
Bruce L. Harding 2004 Nov 16