- Joined
- Aug 14, 2009
- Messages
- 27,494
The pics are (finally!) in!
My reset thread: [URL='https://www.pricescope.com/community/threads/yssies-reset-thread.166349/']https://www.pricescope.com/community/threads/yssies-reset-thread.166349/[/URL]
A big *thank you* to everyone who gave me thoughts, opinions, and advice in that thread!!
Verdict: two more happy Canera customers
Both rings are in nickel-wg. VC matched the colour to my original wedding band (which one of the cats made away with last night, DH and I have a full house search planned for Saturday!), so I can wear all three together. The centre is a 2.7 J, the first pair of sides are the same as from my old ring (0.43 J each), VC provided the second pair of 3.3mms. Rings are size 4.25.
In one of our conversations he told me he thought it was the hardest ring he'd ever made. I posted this paraphrasing of the difficulties he talked about in my other thread:
Looking at it... I think I see his points! The wires were laser welded instead of soldered to avoid colour differences between the gold and the solder. The prongs are edible
and the engraving on the band is so, so delicate and precise...
Precise. That's the word. Handforged does *not* need to be synonymous with lack of precision in design or finish, even with nitpicky designs... I have proof!
Alrighty, on to the stuff people actually care about
This is how it started:
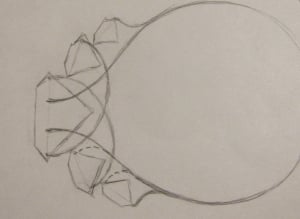
My reset thread: [URL='https://www.pricescope.com/community/threads/yssies-reset-thread.166349/']https://www.pricescope.com/community/threads/yssies-reset-thread.166349/[/URL]
A big *thank you* to everyone who gave me thoughts, opinions, and advice in that thread!!
Verdict: two more happy Canera customers
Both rings are in nickel-wg. VC matched the colour to my original wedding band (which one of the cats made away with last night, DH and I have a full house search planned for Saturday!), so I can wear all three together. The centre is a 2.7 J, the first pair of sides are the same as from my old ring (0.43 J each), VC provided the second pair of 3.3mms. Rings are size 4.25.
In one of our conversations he told me he thought it was the hardest ring he'd ever made. I posted this paraphrasing of the difficulties he talked about in my other thread:
He detailed some of the difficulties in our first email conversation. Basically - what all those tradepeople say about some designs just being better suited to one method of manufacturing than another - is actually true! each individual part starts as a bar of metal, or a cylinder, or a slab, that he shapes properly and solders into place. The shank of my design is plain, so that's easy I guess, but the head is a trellis - so however many long cylinders that need to be bent perfectly to twirl around and between each other, soldered exactly symmetrically on L/R and front/back, with minimal room for error since the elements are close enough together that even a mm off would be glaring. Then there's the fact that I want it made specifically in Ni-wg, which is a hard metal - harder to bend and mould than plat., and gold solder is a slightly different colour so the solder joints would have to be well-hidden (mostly on the interior I guess) so that they aren't noticeable. Then there's the perfection of finish, prongs, polish inside and out that his customers have come to expect on all his pieces...
Looking at it... I think I see his points! The wires were laser welded instead of soldered to avoid colour differences between the gold and the solder. The prongs are edible



Precise. That's the word. Handforged does *not* need to be synonymous with lack of precision in design or finish, even with nitpicky designs... I have proof!
Alrighty, on to the stuff people actually care about
This is how it started:
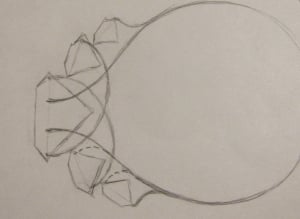