This will repeat material that got lost at the end of another thread, among unrelated conversation between other members. It is too important to get lost like that.
I don't yet know how diamond scanners work, but this shows what they see if looking at a profile, as in a 'shadowgraph' machine used in industry for inspection, or the old GIA ProportionScope.
Here is a pic of what a scanner sees if viewing a profile according to the direction of the ideal index, when a main has been cut at a shifted azimuth. In this example one main was cut at 1° from ideal index (or azimuth), and therefore at a steeper slope (40.960°) to maintain the same join with the neighboring main on its left side.
In this case the scanner will see the left edges of the main, which show a bend in the profile (red) on the image plane - see enlarged view at lower left. The upper segment (join between mains) is still at 40.75° (because the slope of the twisted facet was chosen to maintain this edge of the ideal cut), but this is not the slope of the main in question. The lower segment is at slope of 41.007°, which is also a false indication.
On the other hand, if the scanner looks only at the top and bottom end of the facet, and assumes a straight line between them, it would say 40.956° if it could measure that accurately, which would also be a false indication.
Only if the scanner looks at the actual 1°-shifted index, parallel to its trace (red line in girdle plane), will it see a straight profile and the true slope - by profile and/or tip-to-tip - of 40.960°.
Is this significant? That's for you to decide. I think that one decimal place is suitable for reports, in which case 40.960°, 40.956° and 41.007° would all round-off to 41.0°. The 40.75° indication would be unacceptable and the machine or user would have to ignore it.
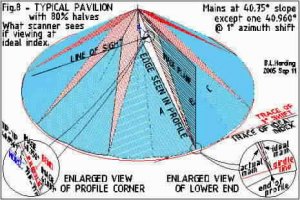
I don't yet know how diamond scanners work, but this shows what they see if looking at a profile, as in a 'shadowgraph' machine used in industry for inspection, or the old GIA ProportionScope.
Here is a pic of what a scanner sees if viewing a profile according to the direction of the ideal index, when a main has been cut at a shifted azimuth. In this example one main was cut at 1° from ideal index (or azimuth), and therefore at a steeper slope (40.960°) to maintain the same join with the neighboring main on its left side.
In this case the scanner will see the left edges of the main, which show a bend in the profile (red) on the image plane - see enlarged view at lower left. The upper segment (join between mains) is still at 40.75° (because the slope of the twisted facet was chosen to maintain this edge of the ideal cut), but this is not the slope of the main in question. The lower segment is at slope of 41.007°, which is also a false indication.
On the other hand, if the scanner looks only at the top and bottom end of the facet, and assumes a straight line between them, it would say 40.956° if it could measure that accurately, which would also be a false indication.
Only if the scanner looks at the actual 1°-shifted index, parallel to its trace (red line in girdle plane), will it see a straight profile and the true slope - by profile and/or tip-to-tip - of 40.960°.
Is this significant? That's for you to decide. I think that one decimal place is suitable for reports, in which case 40.960°, 40.956° and 41.007° would all round-off to 41.0°. The 40.75° indication would be unacceptable and the machine or user would have to ignore it.
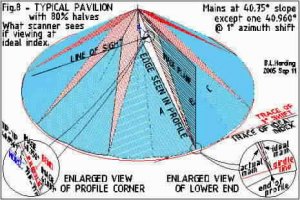