Thanks for taking my comment well.
Cutting the ring out of a solid ingot can be a great way of making a ring, it does take a lot of time and creates a lot of scrap that has to be recycled but it results in a seamless ring that will be very durable and more resestant to warping and scratching than a cast one given that the alloys are the same.
It does require some experence and skill to make the band this way but it is doable and is a realistic expectation within the budget (this will be different from worksshop to workshop), it really isn't all that different carving away metal than it is wax. (in fact I feel more care is needed to carve wax because it is so easy to carve you can very quickly find that you have removed to much material)
For educational purpose here is a picture of a ring I cut out of an ingot, The client wanted a very tall chunkier ring so I found doing it this way worked out well. This is when the piece is first cut out and has had not working to fine it down and put the half round finish on.
Again different workshops may think I'm crazy to do it this way, we are a very small shop with just my Brother an I making our pieces so we can afford the time to put extra labor into our pieces.
Take care, Mike.
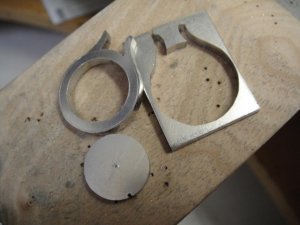
Cutting the ring out of a solid ingot can be a great way of making a ring, it does take a lot of time and creates a lot of scrap that has to be recycled but it results in a seamless ring that will be very durable and more resestant to warping and scratching than a cast one given that the alloys are the same.
It does require some experence and skill to make the band this way but it is doable and is a realistic expectation within the budget (this will be different from worksshop to workshop), it really isn't all that different carving away metal than it is wax. (in fact I feel more care is needed to carve wax because it is so easy to carve you can very quickly find that you have removed to much material)
For educational purpose here is a picture of a ring I cut out of an ingot, The client wanted a very tall chunkier ring so I found doing it this way worked out well. This is when the piece is first cut out and has had not working to fine it down and put the half round finish on.
Again different workshops may think I'm crazy to do it this way, we are a very small shop with just my Brother an I making our pieces so we can afford the time to put extra labor into our pieces.
Take care, Mike.
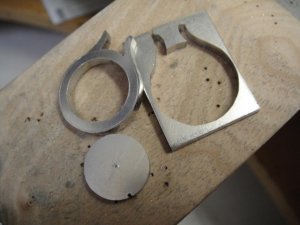